Holger Stichel
A passion for moulds in the name of the snake
Holger Stichel spreads the message about the Vogtland region all over the world
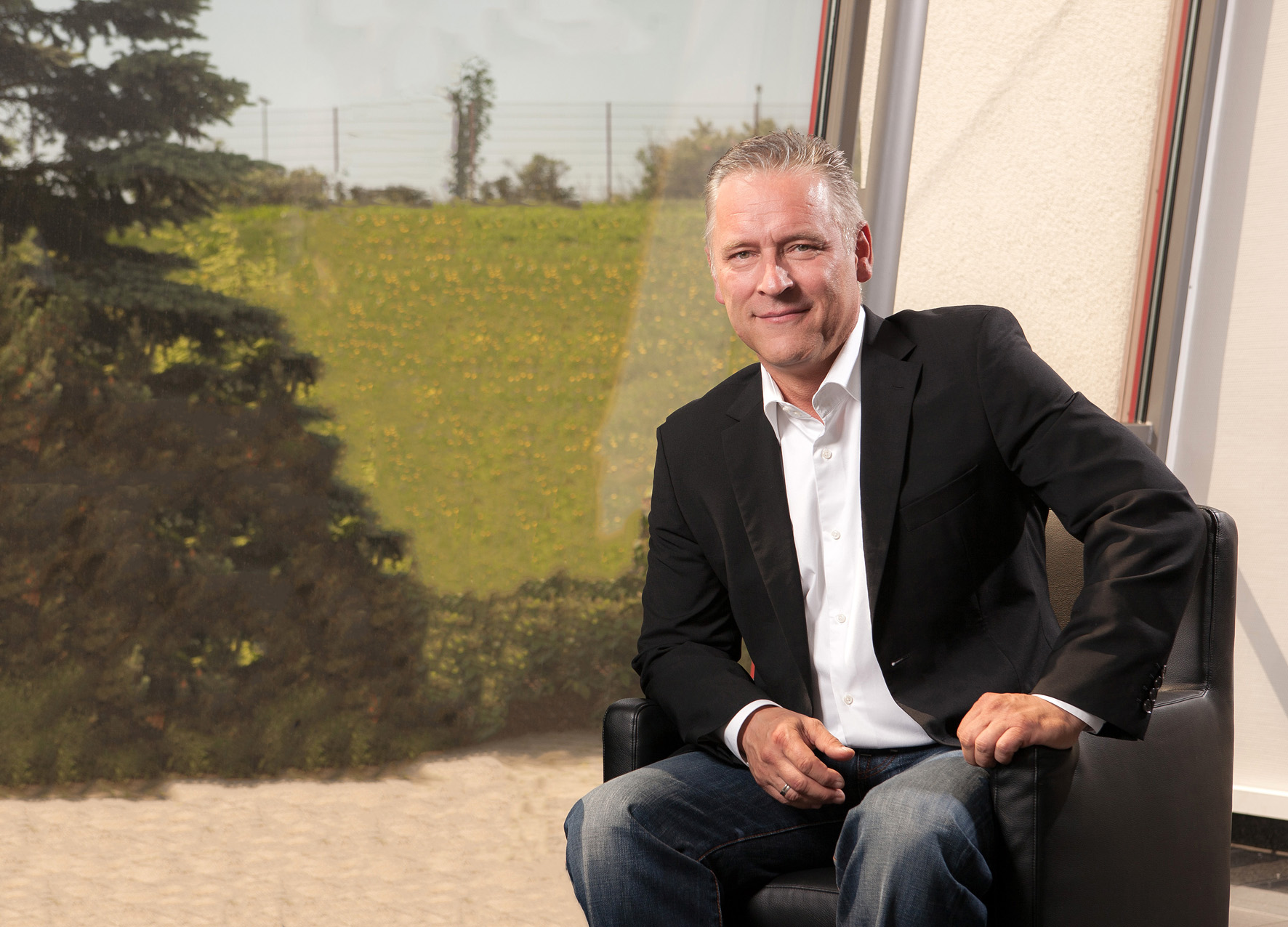
What do you imagine the boss of a global market leader might look like? He probably usually wears a suit, a shirt with a shark collar and a fashionable tie. Holger Stichel offers some kind of alternative to this cliché. The 355 members of staff at Kobra Formen GmbH know their boss, who was born in Chemnitz, as someone who wears jeans and a polo shirt; he has been living in attractive Pechtelsgrün since 2001 and shortly afterwards the then owner Rudolf Braungardt promoted him from the position of technical manager and appointed him as the company’s managing partner.
The 52-year-old is what you might call somebody who has “arrived”. The Vogtland area is the central focus of his life, both professionally and privately. “I enjoy living in a rural, hilly region with friendly neighbours. The residents of our village named me a real “Pechtelsgrüner” two years ago on my 50th birthday – in the Vogtland region, that’s probably the highest award that a newcomer can receive,” says Stichel, laughing; he loves the people in the Vogtland region too. “The people here aren’t as open as other folks, but they’re hard-working, industrious and often superb technical specialists. And when they’ve warmed up, Vogtland people can be open and warm-hearted,” he says, stating his case. He says this, although he knows the world. For Kobra Formen GmbH, which Braungardt set up in Lengenfeld after the fall of the Berlin Wall, has branches all over the world, which primarily handle the sales of the moulds produced in the Vogtland area.
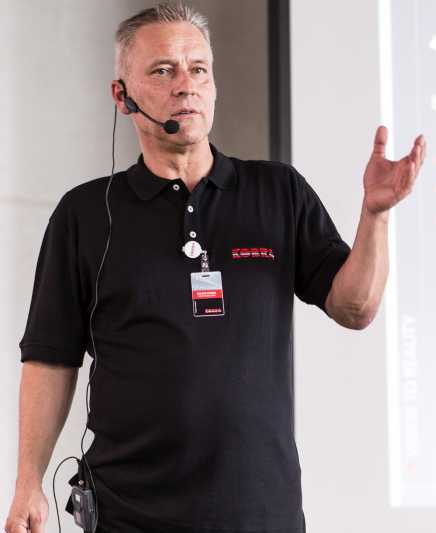
Anybody who has walked across a supermarket car park will certainly have seen the products produced with the special tools, which are “Made in Vogtland”. Nearly all the concrete blocks made by about 1,000 concrete item manufacturers with their approx. 6,000 production sites round the globe are made using block moulds from Lengenfeld. “Nowadays, most concrete blocks are not cast, but mass-produced in a semi-solid state by shaking, ramming and immediate release from the mould. This gives rise to high levels of pressure and many production cycles. The tools used for these have to be extremely durable. They’re precisely the moulds that we manufacture – from the joint draft for a block design with a customer to 3D design work and even the hardening process,” says Stichel – and even as he explains the procedure, you can see his passion for his product. This passion is also what the skilled building worker and graduate engineer associates with his job. Many of the concrete block moulds from Lengenfeld are screwed together in an innovative way, instead of being welded. “This makes us more flexible than most of our competitors. We can achieve technical degrees of hardness at our own hardening shop that bring tears to the eyes of other metalworkers,” Stichel smiles. The adopted ambassador for the Vogtland region entered this sector straight after the fall of the Berlin Wall, set up concrete factories in Eastern Germany and got to know the committed mould makers centred on the company’s founder at the time, Rudolf Braungardt. After spending a short time in north-west Germany, he arrived at Kobra in Lengenfeld. Since that time, he has helped keep the company on course and adapted it to meet the latest requirements. “Particularly the new opportunity of developing three-dimensional surface designs with customers, which they then impress on to the surface of the concrete block, has proved to be a good decision. The demand for this, particularly from medium-sized companies, is huge and we now employ five block designers. We’ve also completely resynchronised the production stages, from the delivery date backwards; we now have parallel production, as it were, where formerly each stage followed another in individual production,” says Stichel, disclosing some of the company’s secrets. “It’s now been possible to almost completely comply with delivery promises given to customers.”
And what about the issue of a shortage of specialist workers? The company is planning to grow and therefore needs committed, competent people; it has been regularly training them for twenty years or doing so with the universities of cooperative education in Glauchau and Plauen. “At least 120 of our current members of staff have already passed through our own training workshop,” says Stichel with a sense of pride that his employees are almost all young Vogtland people, who are also paid a decent wage.
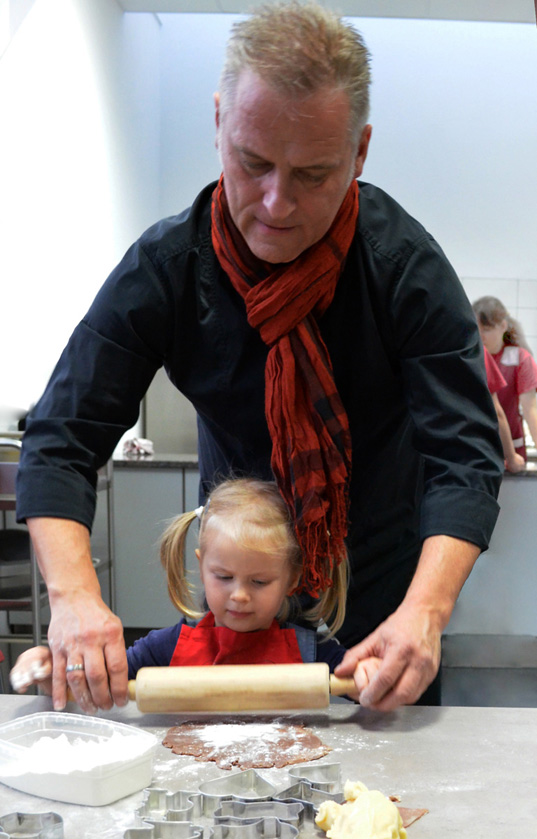
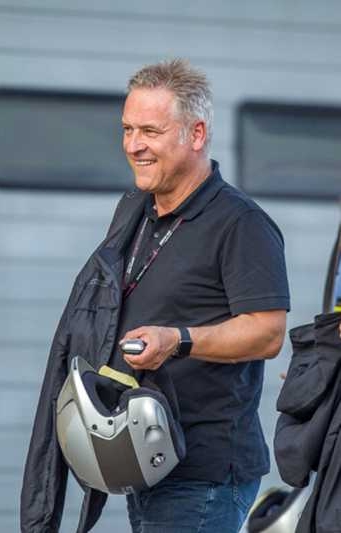
This whole package is certainly the reason why he feels so much at home in the region. He is the head of the village’s young people’s and sports association in Pechtelsgrün and he devotes some of his rather limited free time to this. Because of his love of technology, he says his hobby is motor racing. “It always sounds a bit aloof, but it’s just great to roar round the Sachsenring circuit with an outrageously expensive AMG bullet,” he says; the married father of two – he even has one grandchild – oozes emotion when he talks about his very special passion.
Personal details
Vita Holger Stichel
- Born in Karl-Marx-Stadt
- Married with two children
- Vocational training with final school-leaving exams
- Studied engineering in Karl-Marx-Stadt
- Established concrete factories in Eastern Germany after the fall of the Berlin Wall (ABS Cottbus, Skipiol)
- Managing Director of BEQU-System GmbH in Paderborn
- Technical Manager at Kobra Formen GmbH since 2001
- Managing Partner at Kobra Formen GmbH